Composite Cladding Manufacturer Issues Product EPD
With its highly recycled Wildwood cladding, this company puts its EPD on display.
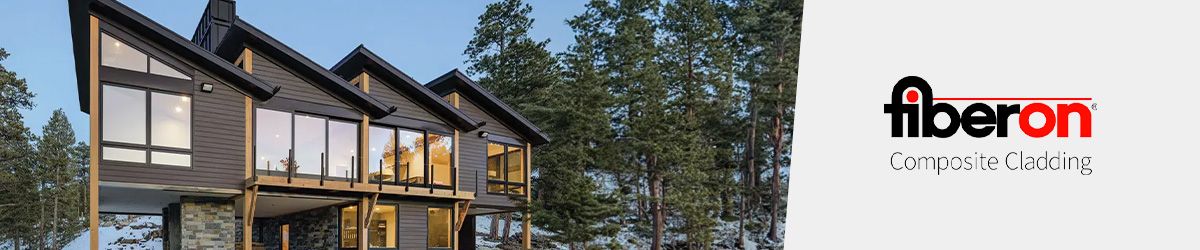
With its highly recycled Wildwood cladding, this company puts its EPD on display.
Fiberon takes pride in being among the first to do anything. Issuing an Environmental Product Declaration (EPD) for its Wildwood composite cladding is a prime example.
The New London, N.C.-based company is one of the first composite manufacturers to release such an EPD, which offers a detailed look at the environmental impact of Wildwood, including raw material extraction, manufacturing and product disposal. The life cycle assessment confirmed that the wood-plastic cladding meets the environmental ISO standards required of products used in LEED v4-certified builds.
All seven of Fiberon’s decking and cladding product lines now have EPDs, according to Fiberon Marketing Specialist Jacob Szypka. “Our customers have a lot of great reasons to choose Fiberon composite decking over pressure-treated lumber,” he says. “When we decided to pursue an EPD, we didn’t view it as an opportunity to raise our prices but to instead introduce our products to a broader market that was looking for an alternative to wood backed by a sustainability story [people] can feel good about.”
Wildwood’s manufacturing facility uses a closed-loop water system, which prevents enough water to fill 5,300 Olympic-size swimming pools from ending up in the waste stream. The composite boards are made with at least 94 percent recycled materials, including both wood and plastic. With this approach, Fiberon saves more than 1 million trees from being cut down each year and recycles an average of 100 million pounds of plastic annually, the company notes.
While traditional wood cladding is pressure-treated with chemicals and requires regular refinishing, Wildwood never needs to be sanded, stained or painted, which supports healthier air quality throughout its lifetime. The durable composite core of Wildwood ensures exceptional resistance to rotting, cracking, insects and decay.
Fiberon is one of the largest recyclers of polyethylene in the United States. The company has been open about how its products are manufactured and the environmental benefits of their creation. But there is no need to take only Fiberon’s word for it. “While our story provides insight into our manufacturing process, we felt we had an obligation to be transparent with our customers by having that process reviewed by a third party,” Szypka notes.
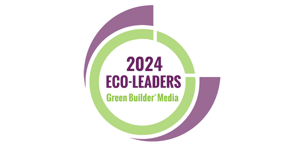
Quick Stats
- Plastic bags diverted from the landfill annually: 2,000
- Swimming pools filled with water diverted from the waste stream: 5,300
- Percent of recycled materials used for Wildwood cladding: 94
That third party, SCS Global Services, is well known for its diligence when considering a company’s product for an EPD. “We are striving to advance sustainable development goals through independent assessment, the application of sound science, and innovative solutions,” the company notes. “Through these services, we are enabling decision-makers and purchasers to make informed decisions, giving innovators a competitive edge, and helping to drive the development of leadership standards to create a framework for continuous improvement.”
According to Szypka, an EPD has become a strong marketing tool. The company constantly receives viewing requests from domestic and international customers. Those requests are expected to increase as environmental impact becomes a greater focus within the construction industry.
But above all, obtaining an EPD was simply “the next logical step in becoming an eco-leader,” Szypka notes. “Fiberon is focused on continuing to improve our process and offering a premium product our customers are proud to own.”
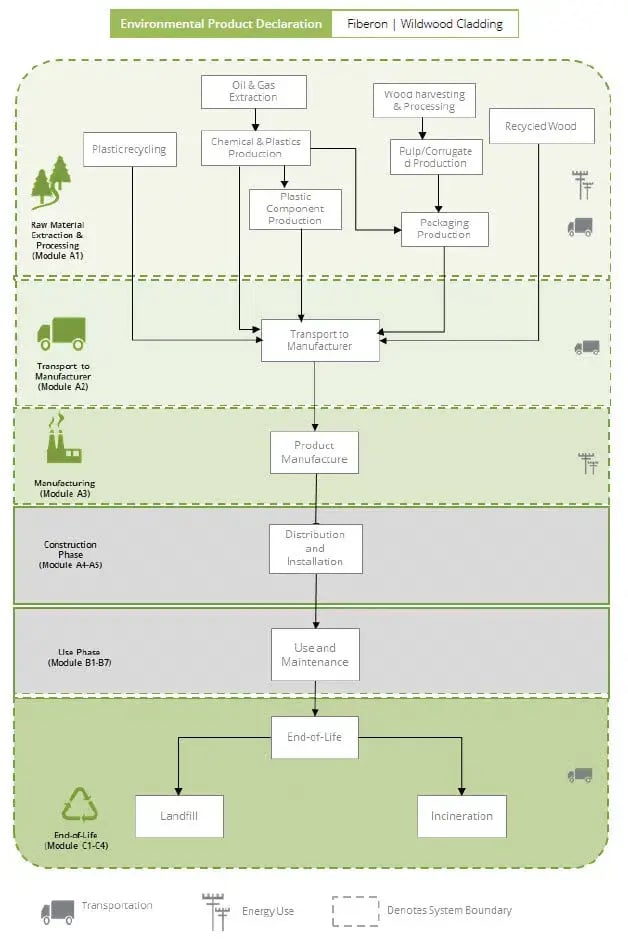